Why Use UV Resin for Hologram Casting?
- Guri Dhillon
- 1 hour ago
- 2 min read
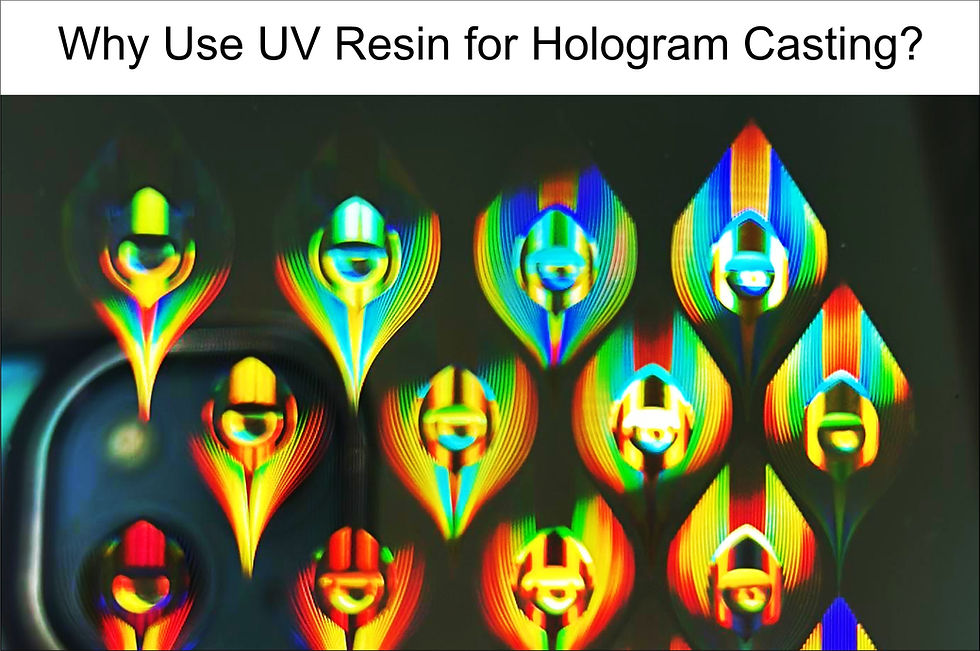
UV resin is the preferred material for hologram casting because of its high precision, fast curing, and excellent optical properties. Here’s why UV resin is widely used in security holograms, diffractive optical elements (DOEs), and high-resolution embossing applications.
1. Fast Curing with High Precision
Instant Hardening: UV resin cures within seconds when exposed to UV light, allowing for rapid production.
High Detail Reproduction: The fast curing ensures that fine holographic structures (in the nanometer range) are perfectly replicated from the master mold.
Why it matters?
Ensures sharp and clear holographic effects.
Supports high-speed manufacturing for large-scale production.
2. Excellent Optical Clarity
UV resins are highly transparent, allowing maximum diffraction efficiency for holograms.
Low haze and minimal distortion help maintain the brightness and sharpness of the holographic image.
Why it matters?
Produces vibrant, high-contrast holograms with better visibility.
Prevents image blurring or loss of holographic detail.
3. High Refractive Index for Enhanced Diffractive Effects
Many UV resins are formulated with a high refractive index (RI), which is critical for stronger and brighter holographic visuals.
A higher RI ensures better light diffraction, leading to more pronounced holographic colours.
Why it matters?
Improves viewing angles and colour shifting effects.
Makes holograms harder to counterfeit due to unique optical properties.
4. Durability & Environmental Stability
UV resins create a hard, scratch-resistant surface once cured.
Many formulations offer moisture and chemical resistance, ensuring long-lasting holograms.
Some UV resins are also heat-resistant, making them ideal for security applications.
Why it matters?
Ensures holograms stay intact over time, even in harsh environments.
Reduces the risk of wear and tampering.
5. Versatile for Different Substrates
UV resin can be used on various materials, including plastic films, glass, metal, and paper.
It adheres well to polycarbonate (PC), polyethylene terephthalate (PET), and other flexible films used in banknotes, ID cards, and packaging.
Why it matters?
Enables hologram application on diverse products.
Compatible with roll-to-roll and batch production processes.
6. Ideal for Mass Production & Roll-to-Roll Processes
UV resin is suitable for roll-to-roll (R2R) processing, enabling continuous high-speed hologram production.
This makes it cost-effective and scalable for commercial applications.
Why it matters?
High-volume hologram manufacturing for security foils, stickers, and anti-counterfeiting labels.
Lowers production costs while maintaining high quality.
7. Customization & Formulation Flexibility
UV resins can be engineered for specific needs, such as:
Flexible or rigid properties
Different refractive indices
Varying thickness and viscosity for different applications
Why it matters?
Custom resins allow tailored security features for different industries, including banknotes, passports, and brand protection.
Using UV resin for hologram casting ensures high precision, optical clarity, durability, and fast production, making it the gold standard for security applications. With its ability to reproduce fine holographic structures and support mass production, UV resin is the ideal choice for industries needing anti-counterfeiting, authentication, and decorative holographic effects.
Written for general awareness by team at www.xrdnano.com
Comments